SolderTips: Issues With Incomplete Solder Reflow in Production
How Can We Help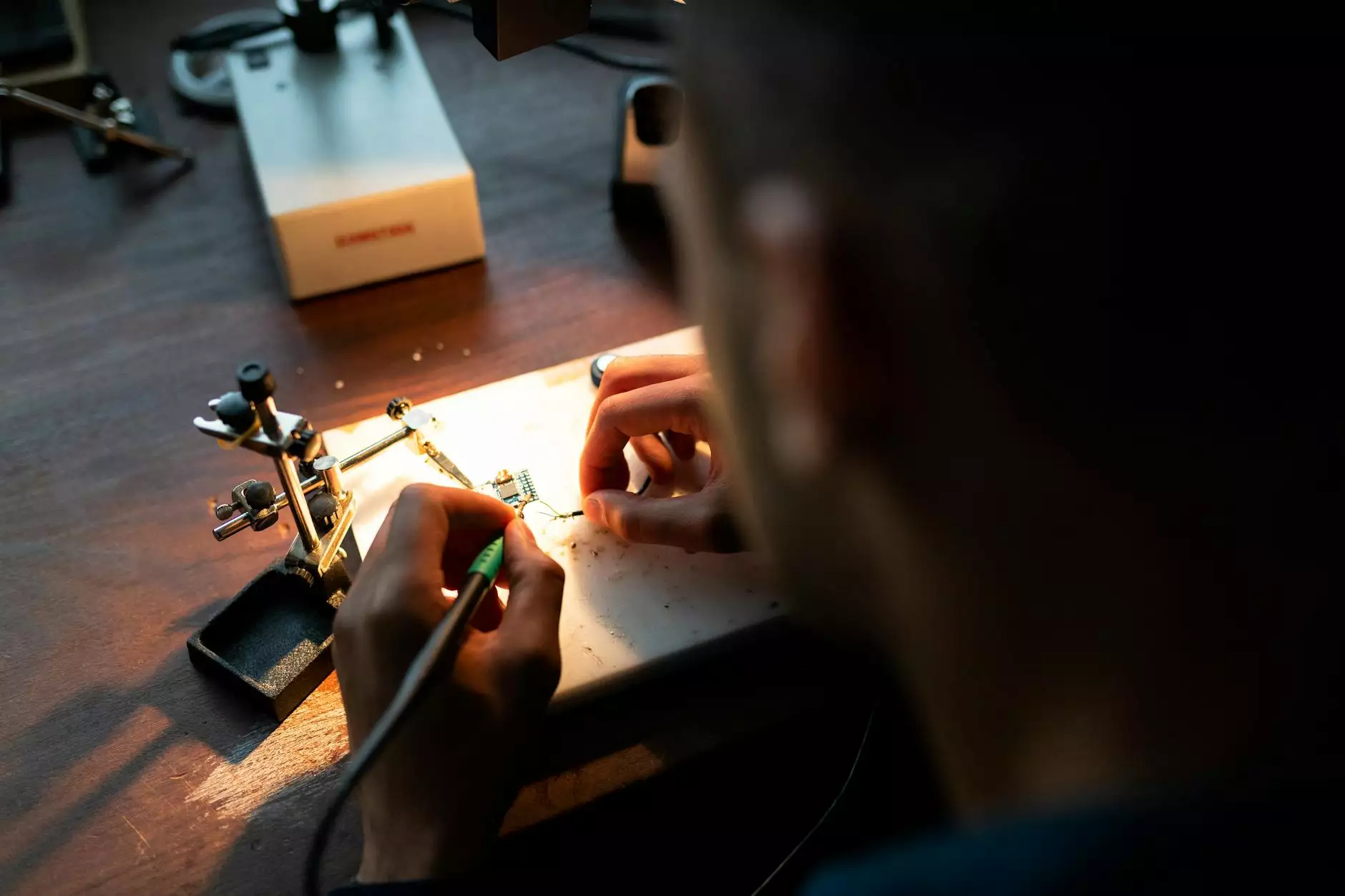
Introduction
Are you experiencing incomplete solder reflow in your production process? Look no further! At SolderTips, we understand the challenges that come with solder reflow, and we are here to help you overcome them. In this comprehensive guide, we will explore the common issues faced during the solder reflow process and provide you with valuable tips to achieve complete solder reflow for optimal results.
Understanding Incomplete Solder Reflow
Solder reflow is a critical step in electronic manufacturing. It involves melting solder paste to create reliable and electrically conductive connections between components on a printed circuit board (PCB). However, incomplete solder reflow can lead to various problems, including weak solder joints, decreased reliability, and performance issues. It is crucial to identify and address the factors causing incomplete solder reflow to ensure the production of high-quality electronic assemblies.
Common Issues with Incomplete Solder Reflow
Let's dive into some of the common issues encountered during solder reflow that result in incomplete solder reflow:
1. Insufficient Preheat
Insufficient preheating of the PCB and components can lead to incomplete solder reflow. It is essential to bring the assembly to the recommended temperature before entering the reflow zone. Insufficient preheating can lead to incomplete wetting, resulting in poor solder joint formation.
2. Incorrect Profile Settings
Using incorrect temperature profiles in the reflow oven can cause incomplete solder reflow. Each solder paste has specific reflow profile recommendations. Deviating from these recommended settings can adversely affect solder paste performance, resulting in incomplete reflow.
3. Uneven Heating
Uneven heating within the reflow oven can cause incomplete solder reflow. This could be due to inadequate convection or radiant heat distribution. It is crucial to ensure proper airflow and heat distribution within the oven to achieve consistent solder reflow across the entire PCB.
4. Deteriorated Solder Paste
Solder paste has a shelf life, and using expired or deteriorated solder paste can lead to incomplete reflow. Expired solder paste may not melt properly, resulting in incomplete wetting and weak solder joints. Ensuring the use of fresh solder paste is essential for consistent solder reflow.
5. Insufficient Flux Activity
Flux is a crucial component of solder paste and plays a vital role in the reflow process. Insufficient flux activity can hinder proper wetting and affect the overall solder reflow. It is important to use high-quality solder paste with adequate flux activity to ensure complete solder reflow.
Tips for Achieving Complete Solder Reflow
1. Optimize Preheating
Ensure proper preheating of the PCB and components before entering the reflow zone. This will help prevent thermal shock and uneven heating, resulting in complete solder reflow. Follow the recommended preheating temperature and time specifications provided by your solder paste manufacturer.
2. Fine-Tune Temperature Profile
Review and optimize the reflow oven temperature profile to match the recommended settings provided by your solder paste manufacturer. This will ensure consistent solder reflow across the entire PCB, minimizing the risk of incomplete solder joints.
3. Optimize Oven Heat Distribution
Regularly inspect and maintain your reflow oven to ensure proper airflow and heat distribution. Placement of baffles or adjusting conveyor speed can help achieve even heating, minimizing the chances of incomplete solder reflow.
4. Use Fresh Solder Paste
Always check the expiration date of your solder paste and ensure its freshness. Using fresh solder paste will help maximize flux activity and improve solder wetting, resulting in complete solder reflow.
5. Verify Flux Activity
Perform regular flux activity tests to ensure the effectiveness of your solder paste. This will help identify any issues with flux activity and allow you to make necessary adjustments for optimal solder reflow.
Conclusion
Incomplete solder reflow can be a frustrating and costly problem in electronic manufacturing. By understanding the common issues and following our tips for achieving complete solder reflow, you can overcome these challenges and produce high-quality electronic assemblies. Remember, optimizing preheating, fine-tuning temperature profiles, improving oven heat distribution, using fresh solder paste, and verifying flux activity are key to achieving successful and reliable solder reflow in your production process. Trust SolderTips to guide you every step of the way towards achieving optimum solder reflow results!