Issues of Burnt Flux on Class 3 PCB Assemblies
Products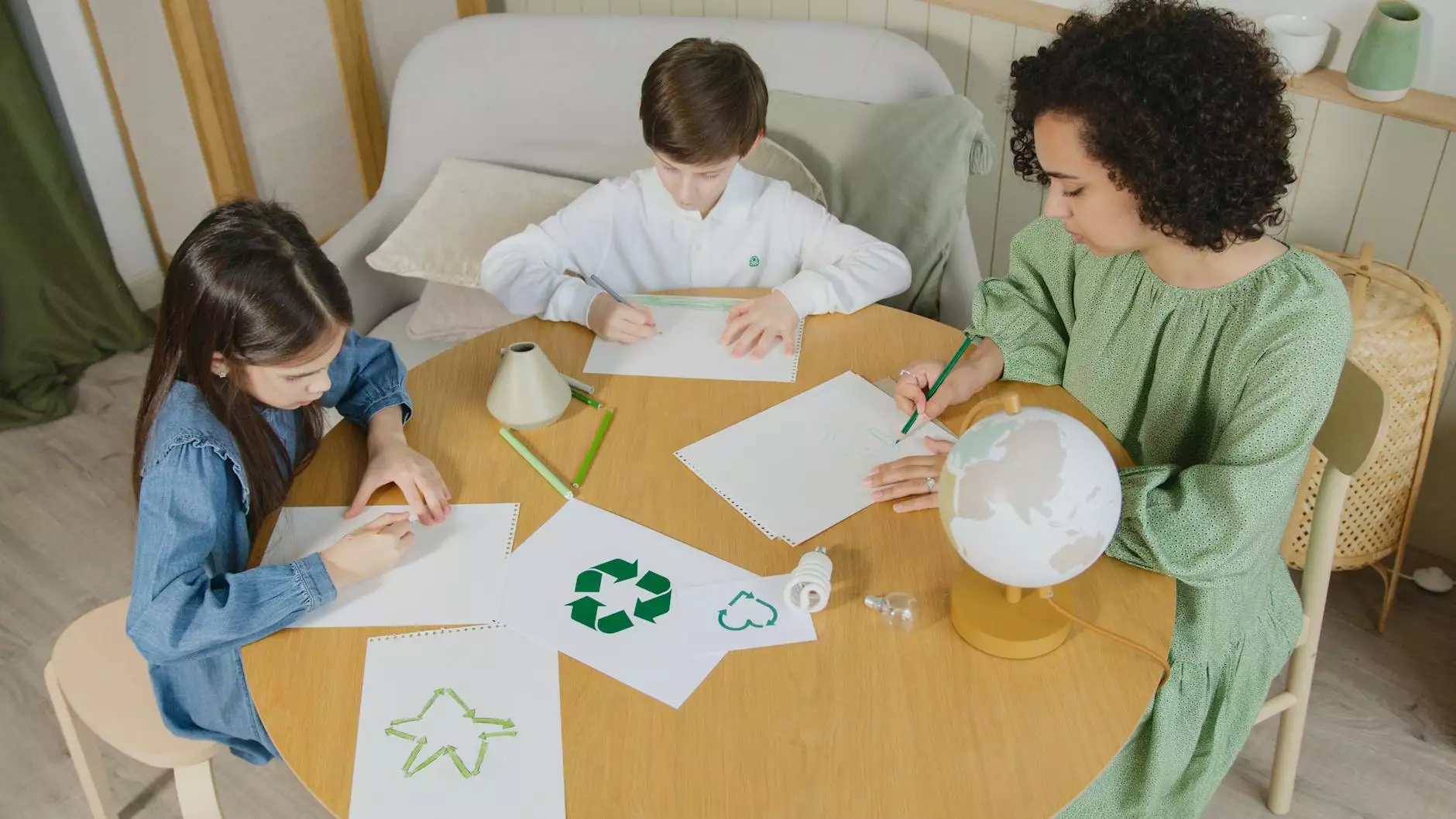
Welcome to Luxury Ride Dubai FAQs! In this section, we will discuss the common issues related to burnt flux on Class 3 PCB Assemblies. As a leading provider in the eCommerce & Shopping - Vehicles & auto parts category, we aim to provide our customers with comprehensive information to help them understand potential challenges and find effective solutions. If you are interested in renting luxury cars such as Audi R8 Coupe V10 or Lamborghini Urus in Dubai, our team is dedicated to making your dreams come true. But now, let's delve into the technical aspects of burnt flux on Class 3 PCB Assemblies.
Understanding Burnt Flux on Class 3 PCB Assemblies
Flux is an essential component in the soldering process of printed circuit boards (PCBs). It works by removing any surface oxide build-up, enabling proper adhesion for the solder to bond with the components and the PCB. However, if the flux is exposed to excessive heat during the soldering process, it can lead to burnt flux issues on Class 3 PCB Assemblies.
Common Causes of Burnt Flux
Several factors can contribute to burnt flux on Class 3 PCB Assemblies:
- High soldering temperatures: When the soldering temperature exceeds the recommended range, the flux can burn, resulting in compromised electrical connections and potential damage to the PCB components.
- Insufficient flux application: Inadequate flux coverage during the soldering process can lead to localized overheating and burnt flux.
- Excessive soldering time: Prolonged exposure to high soldering temperatures can cause the flux to burn, affecting the overall solder joint quality.
- Flux contamination: If the flux used contains impurities or contaminants, it may have a lower threshold for heat exposure, increasing the chance of burnt flux.
- Poor flux storage conditions: Improper storage of flux can result in its degradation, making it more susceptible to burning during soldering.
Identifying Symptoms of Burnt Flux
Recognizing the symptoms of burnt flux on Class 3 PCB Assemblies is crucial for prompt detection and resolution. Some common signs include:
- Pungent odor during or after the soldering process
- Discoloration or dark spots around the solder joints
- Poor or intermittent electrical connections
- Cracks or other physical damages on the PCB surface
- Malfunctioning or non-functional components
Preventive Measures to Avoid Burnt Flux
To prevent burnt flux issues on Class 3 PCB Assemblies, consider the following preventive measures:
- Adhere to recommended soldering temperature and time specifications
- Ensure proper flux application and coverage during the soldering process
- Use high-quality flux from reputable suppliers
- Store flux in a cool, dry place to maintain its integrity
- Regularly inspect PCBs for signs of burnt flux and take immediate action if detected
Conclusion
In summary, understanding the issues related to burnt flux on Class 3 PCB Assemblies is essential for anyone involved in the electronics industry. By recognizing the causes, symptoms, and preventive measures, you can minimize the risk of burnt flux and ensure the reliable performance of your PCB assemblies. At Luxury Ride Dubai, we prioritize the quality and functionality of our luxury vehicles, just as we value the integrity of our PCBs. If you are interested in renting an Audi R8 Coupe V10 or Lamborghini Urus in Dubai, please explore our website for more information. We look forward to providing you with an exceptional experience!