SolderTip #38: Clean vs No-Clean Fluxes
Products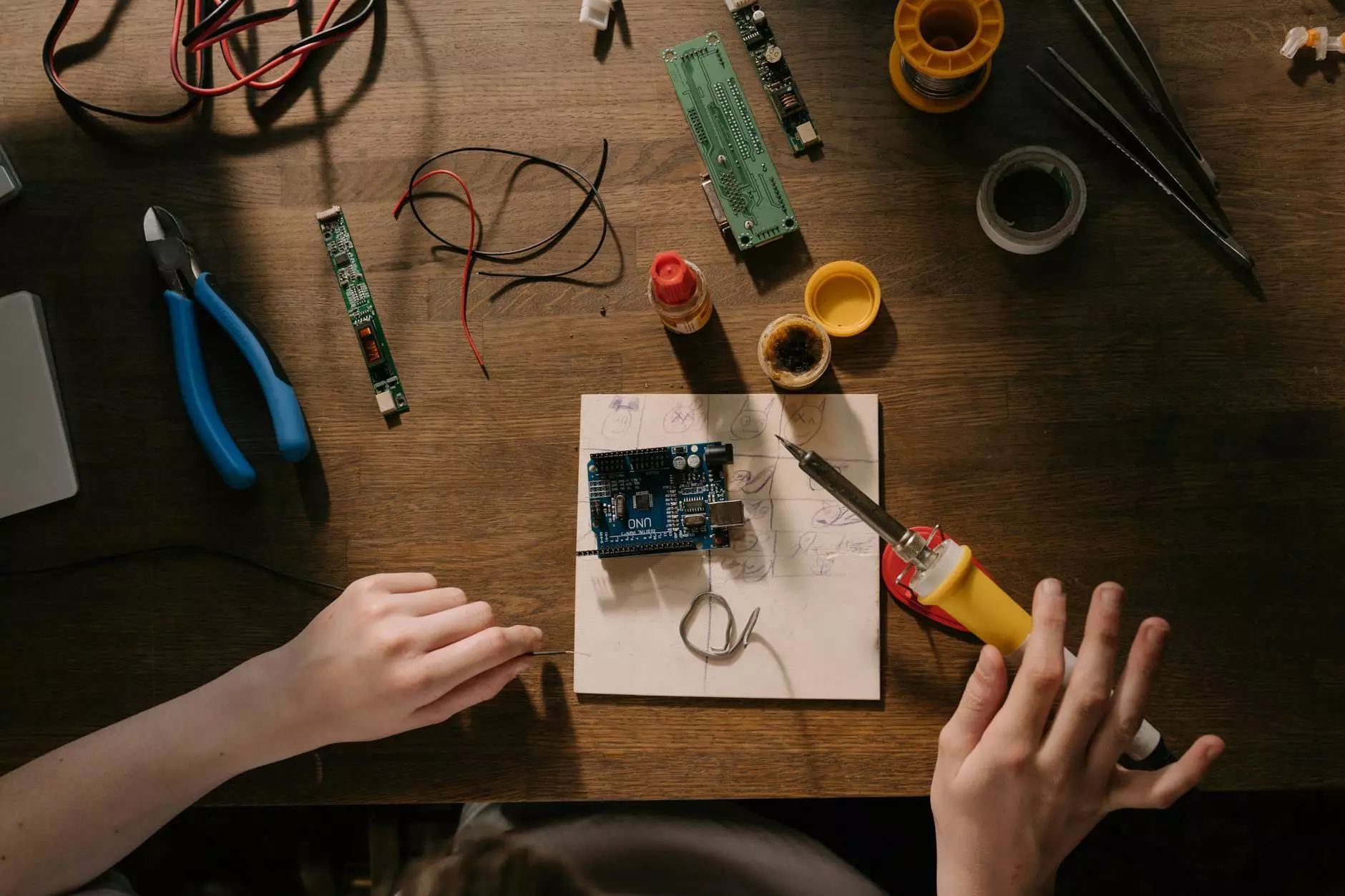
When it comes to soldering, choosing the right flux is crucial for achieving high-quality and reliable solder joints. One of the most common dilemmas faced by soldering enthusiasts is whether to use clean or no-clean fluxes. In this comprehensive guide, we will delve into the key differences between clean and no-clean fluxes, their advantages and disadvantages, and help you make an informed decision for your soldering projects.
Clean Fluxes
Clean fluxes, as the name suggests, are designed to be easy to clean after soldering. They contain a higher percentage of active agents that facilitate the removal of flux residues. Clean fluxes are typically used in applications where post-solder cleaning is desired or necessary, such as in the manufacturing of electronic components or sensitive circuit boards.
Key advantages of clean fluxes:
- Excellent solderability: Clean fluxes offer superb wetting properties, allowing for strong solder joints and minimizing the occurrence of defects.
- No residue: Clean fluxes produce minimal or no residues, ensuring the cleanliness and long-term reliability of soldered connections.
- Easy to clean: The residues left by clean fluxes can be easily removed with an appropriate cleaning agent, leaving behind a pristine solder joint.
Despite their advantages, clean fluxes also have a few potential downsides:
- Additional cleaning steps: Since clean fluxes require post-solder cleaning, extra time and resources may be needed to ensure thorough cleaning.
- Potential for contamination: Improper cleaning or incomplete removal of residues can lead to potential contamination or reliability issues in sensitive electronic applications.
No-Clean Fluxes
No-clean fluxes are formulated to leave behind minimal, if any, residues after soldering. They are widely used in applications where post-solder cleaning is not feasible or required, such as in the repair and rework of electronic assemblies.
Advantages of no-clean fluxes include:
- Simplicity: No-clean fluxes eliminate the need for post-solder cleaning, saving time and resources during the soldering process.
- Reduced risk of contamination: Since no-clean fluxes leave behind minimal residues, the risk of contamination or damage to sensitive components is significantly reduced.
- Improved productivity: The absence of cleaning steps allows for faster turnaround times, making no-clean fluxes a preferred choice in high-volume production environments.
However, it is important to consider the potential drawbacks of using no-clean fluxes:
- Residue visibility: Although no-clean fluxes produce minimal residues, the residues may still be visible, especially on lighter-colored substrates. This can impact the aesthetic appearance of the soldered joints.
- Reliability concerns: While no-clean fluxes are generally reliable for most applications, specific requirements or stringent quality standards may necessitate the use of clean fluxes for optimal long-term performance.
Choosing the Right Flux for Your Application
When deciding between clean and no-clean fluxes, it is essential to consider the specific requirements of your soldering project. Here are some factors to consider:
1. Application type:
Identify whether your application requires post-solder cleaning or if a no-clean solution is acceptable based on the desired level of cleanliness and reliability.
2. Component sensitivity:
If you are working with sensitive components or materials that are prone to contamination, considering clean fluxes might be the safer option.
3. Industry standards:
Ensure you are familiar with any industry standards or regulations that may dictate the use of clean or no-clean fluxes for specific applications.
4. Residue visibility:
If the visual appearance of the soldered joints is crucial, especially in applications where aesthetics matter, opting for clean fluxes might be the more suitable choice.
In conclusion, both clean and no-clean fluxes serve distinct purposes in soldering applications. By understanding their differences and evaluating your specific project requirements, you can make an informed decision on which type of flux to use. Whether you prioritize ease of cleaning, long-term reliability, simplicity, or production efficiency, the right choice of flux will contribute to achieving optimal soldering results.
Remember to consider factors such as application type, component sensitivity, industry standards, and residue visibility when making your decision. If you are unsure or require expert guidance, it is recommended to consult with professionals or trusted suppliers who can provide tailored advice based on your specific needs.
Make your soldering projects a success with the right choice of clean or no-clean flux!