SMT Components During Reflow Float Off Pads
Products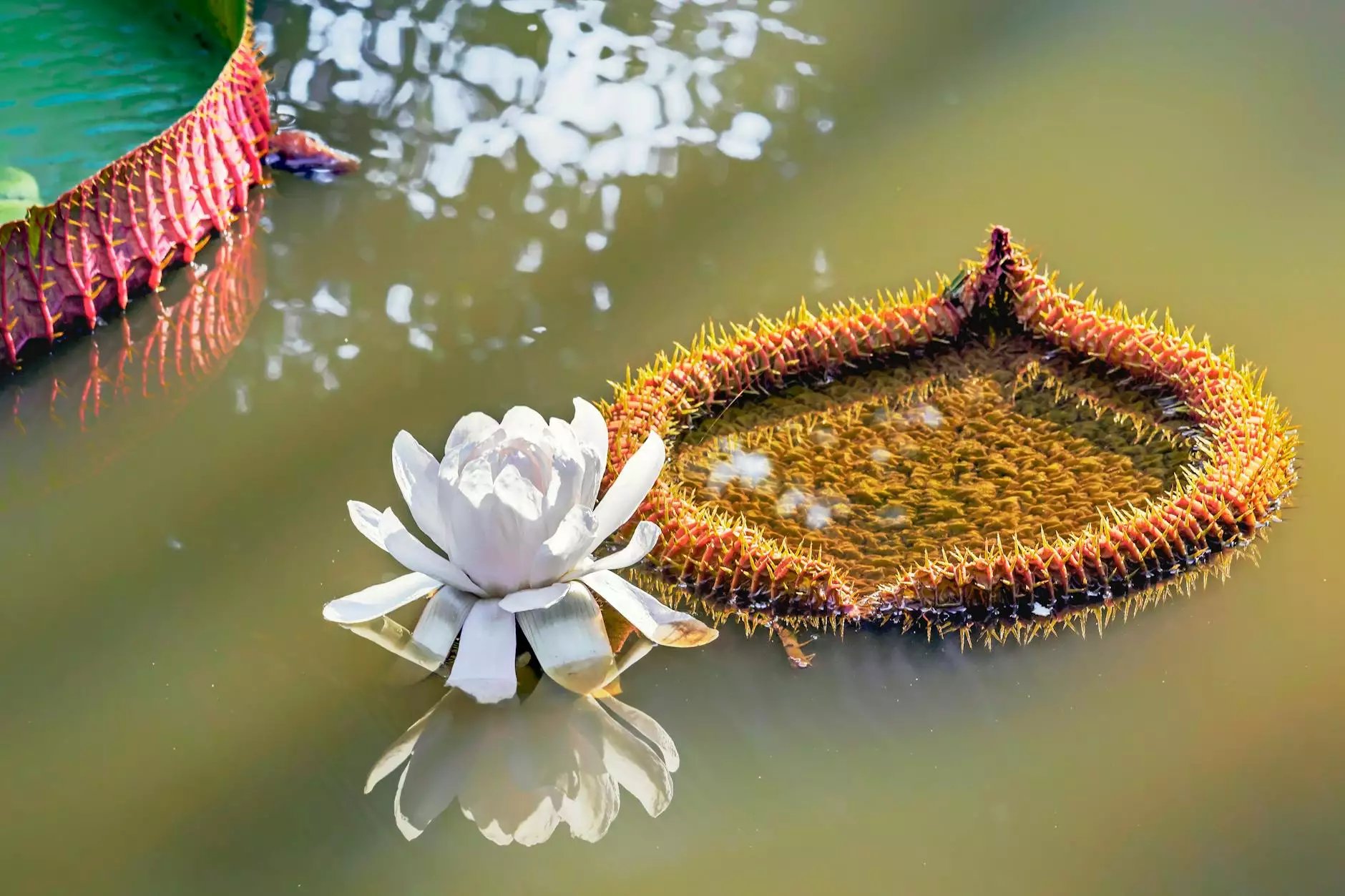
Introduction
When it comes to the reflow process in Surface Mount Technology (SMT), one critical issue to address is the potential of components floating off during reflow. This can cause significant reliability concerns and impact the overall quality of the solder joints. In this article, we will discuss the causes and consequences of float off pads in SMT components during reflow, and explore strategies to mitigate this issue.
Understanding Float Off Pads
Float off pads refer to the phenomenon where SMT components, particularly smaller ones, detach from their intended landing pads during the reflow soldering process. Several factors contribute to this issue, including inadequate solder paste deposition, poor alignment, incorrect component placement, insufficient component adhesion, and excessively high reflow temperatures.
Potential Causes of Float Off Pads
- Inadequate solder paste deposition: Insufficient solder paste deposit on the pads can result in weak connections between the components and the PCB, making them prone to float off during reflow.
- Poor alignment: Incorrect alignment of the components on the landing pads can lead to uneven solder distribution, causing float off during reflow.
- Incorrect component placement: Components placed at incorrect angles or positions may not adhere properly during reflow, increasing the risk of float off.
- Insufficient component adhesion: Insufficient adhesive strength between the components and the pads can cause detachment during the reflow process.
- Excessively high reflow temperatures: Applying excessive heat during reflow can weaken the solder connections, leading to float off issues.
Consequences of Float Off Pads
The consequences of float off pads can be severe, affecting the overall reliability and functionality of the electronic device. Some of the potential consequences include:
- Reduced electrical conductivity: Float off pads can result in poor electrical connections, leading to signal integrity issues and decreased device performance.
- Intermittent or complete failure: Detached components may cause intermittent failures or complete device malfunction.
- Increased repair costs: Float off pads often necessitate rework or repairs, adding to the overall production costs.
- Reduced lifespan: Unreliable solder joints resulting from float off can significantly reduce the lifespan of the electronic device, affecting customer satisfaction and trust.
- Negative impact on brand reputation: Poor product quality due to float off pads can tarnish a company's reputation and credibility in the market.
Strategies to Mitigate Float Off Pads
Preventing float off pads requires a comprehensive approach that addresses several factors throughout the PCB assembly process. Here are some effective strategies to mitigate this issue:
1. Optimizing Solder Paste Deposition
Ensuring adequate solder paste deposition on the landing pads is crucial to achieving strong solder connections. Proper stencil design and optimization of the solder paste printing process can enhance the solder volume and distribution, minimizing the risk of float off.
2. Precision Component Placement
Accurate component placement is essential to achieving optimal solder joint formation. Proper equipment calibration, well-maintained pick-and-place machines, and regular inspection of component placement accuracy can significantly reduce float off risks.
3. Adequate Component Adhesion
Enhancing component adhesion is vital to preventing float off pads. Selecting appropriate adhesives and ensuring proper curing are crucial steps in minimizing float off risks. Additionally, maintaining suitable humidity levels and controlling the moisture absorption properties of components can also improve adhesion.
4. Optimum Reflow Profile
Developing an optimized reflow profile is essential for maintaining the proper balance between achieving thorough solder melting and reducing the risk of float off. By carefully controlling the temperature and time spent above the solder's melting point, float off issues can be minimized.
5. Inspection and Quality Control
Implementing rigorous inspection and quality control procedures can help identify and address float off risks early in the production process. Regular inspection of component placement, solder joint quality, and reflow process parameters can help detect and rectify potential float off issues.
6. Collaboration with Component Suppliers
Collaborating with component suppliers can provide valuable insights into component design and adherence. By working closely with suppliers, manufacturers can ensure the selection of suitable components that are less prone to float off.
Conclusion
Float off pads in SMT components during reflow can have significant consequences on the overall reliability and quality of electronic devices. By implementing the strategies outlined in this article, manufacturers can mitigate the risks associated with float off, improve product reliability, and maintain customer satisfaction. Through careful attention to solder paste deposition, component placement, adhesion, reflow profiles, inspection, and collaboration with suppliers, the float off issue can be effectively minimized, resulting in higher-quality electronic assemblies.