Understanding Solderability Testing for Printed Circuit Boards and Components
Products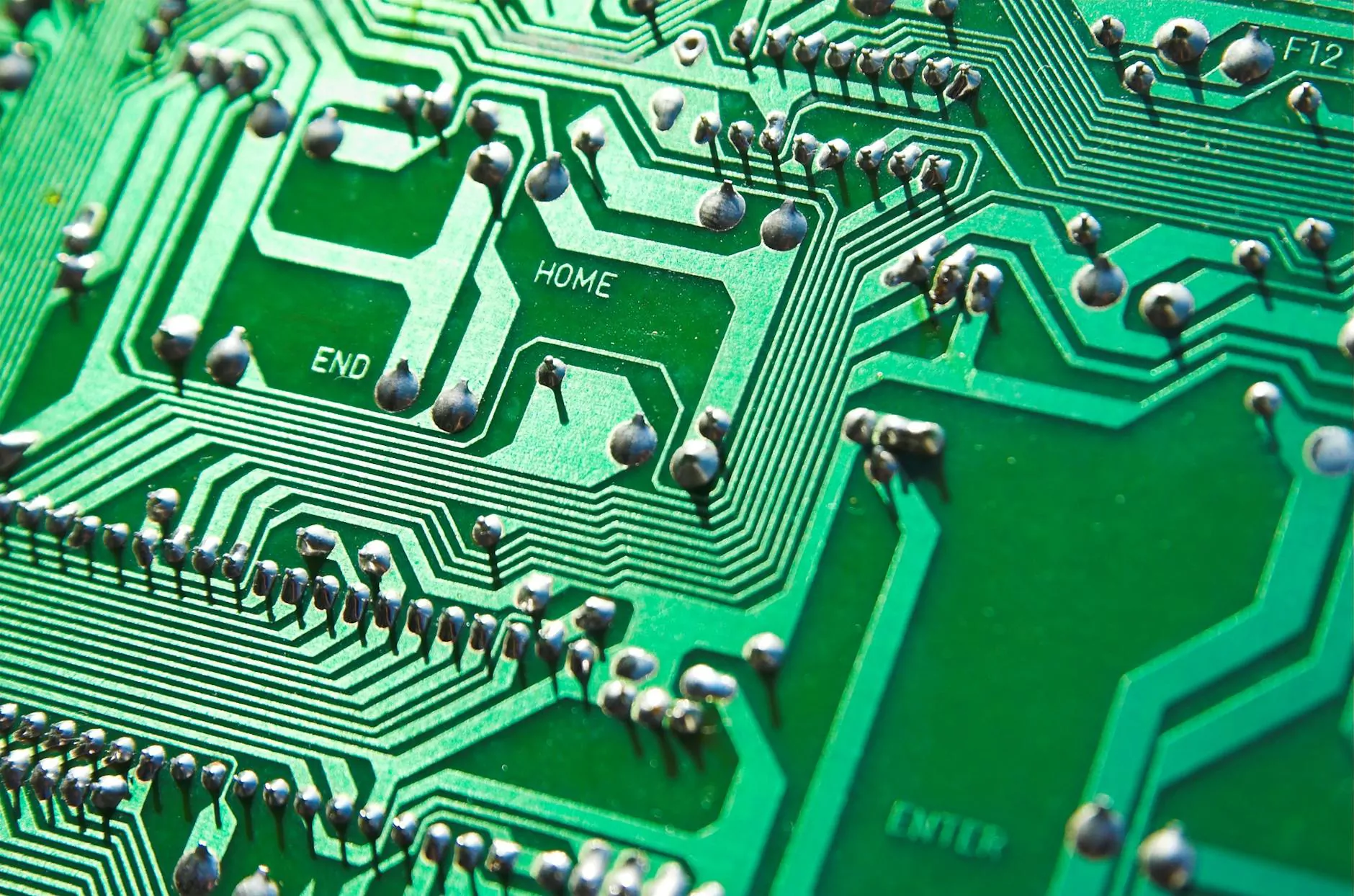
Introduction
Welcome to our comprehensive guide on solderability testing for printed circuit boards and components. In this article, we will delve into the details of testing methods, industry standards, and best practices to help you gain a deeper understanding of this critical process.
What is Solderability Testing?
Solderability testing is an essential quality control procedure in the electronics manufacturing industry. It assesses the ability of electronic components and printed circuit boards (PCBs) to form a reliable solder joint during the soldering process. By conducting thorough solderability testing, manufacturers can identify potential issues that may impact the overall soldering performance.
Testing Methods
1. Wetting Balance Test
The wetting balance test measures the wetting forces between the solder and the surface of the PCB or component leads. It provides valuable insights into the wettability and adhesion properties of the materials involved. This test involves applying a solder alloy (commonly solder paste) to the specific surface and measuring the force required to separate the solder from the surface. It is a widely-used method due to its accuracy and repeatability.
2. Solder Dip Test
The solder dip test, also known as the dip and look method, examines the solderability of components. It involves immersing the component leads in molten solder and then visually inspecting the quality of solder coverage. The solderability is evaluated based on the extent of coverage, absence of defects, and the formation of proper joints.
3. Thermal Cycling Test
Thermal cycling testing exposes the PCB or component to a series of temperature cycles. This test simulates the conditions the materials will experience during their lifetime. By subjecting them to repeated heating and cooling, potential issues such as thermal stress, solder joint fatigue, and material degradation can be detected.
Industry Standards
Various industry standards and specifications govern solderability testing to ensure the reliability and compatibility of electronic components and PCBs. These standards are set by organizations such as the International Electrotechnical Commission (IEC), the Institute of Electrical and Electronics Engineers (IEEE), and the Joint Electron Device Engineering Council (JEDEC). Compliance with these standards helps manufacturers maintain consistent quality and compatibility across products.
Best Practices
1. Proper Storage and Handling
Ensuring proper storage and handling of electronic components and PCBs is crucial to maintaining their solderability. Components should be stored in controlled environments that are free from moisture and contaminants. Additionally, manufacturers should train their personnel to handle the materials with care, using appropriate ESD (Electrostatic Discharge) precautions to prevent damage.
2. Surface Preparation
Effective surface preparation is vital for achieving good solderability. PCBs and component leads should be thoroughly cleaned and free from oxidation, flux residues, and other contaminants. Various cleaning methods, such as ultrasonic cleaning and chemical cleaning, can be employed depending on the specific requirements.
3. Testing Frequency
Regular testing throughout the manufacturing process is critical to identifying potential solderability issues early on. Conducting tests at different stages, including incoming inspection, during assembly, and post-reflow, allows for continuous monitoring and prompt corrective actions when necessary.
Conclusion
In conclusion, understanding solderability testing for printed circuit boards and components is key to ensuring the quality and reliability of electronic products. By employing appropriate testing methods, adhering to industry standards, and implementing best practices, manufacturers can mitigate the risks associated with poor solderability. Continuous improvement and attention to detail in this essential manufacturing process contribute to the overall success and longevity of electronic devices.