Are Voids in Solder Joints Really an Issue?
Blog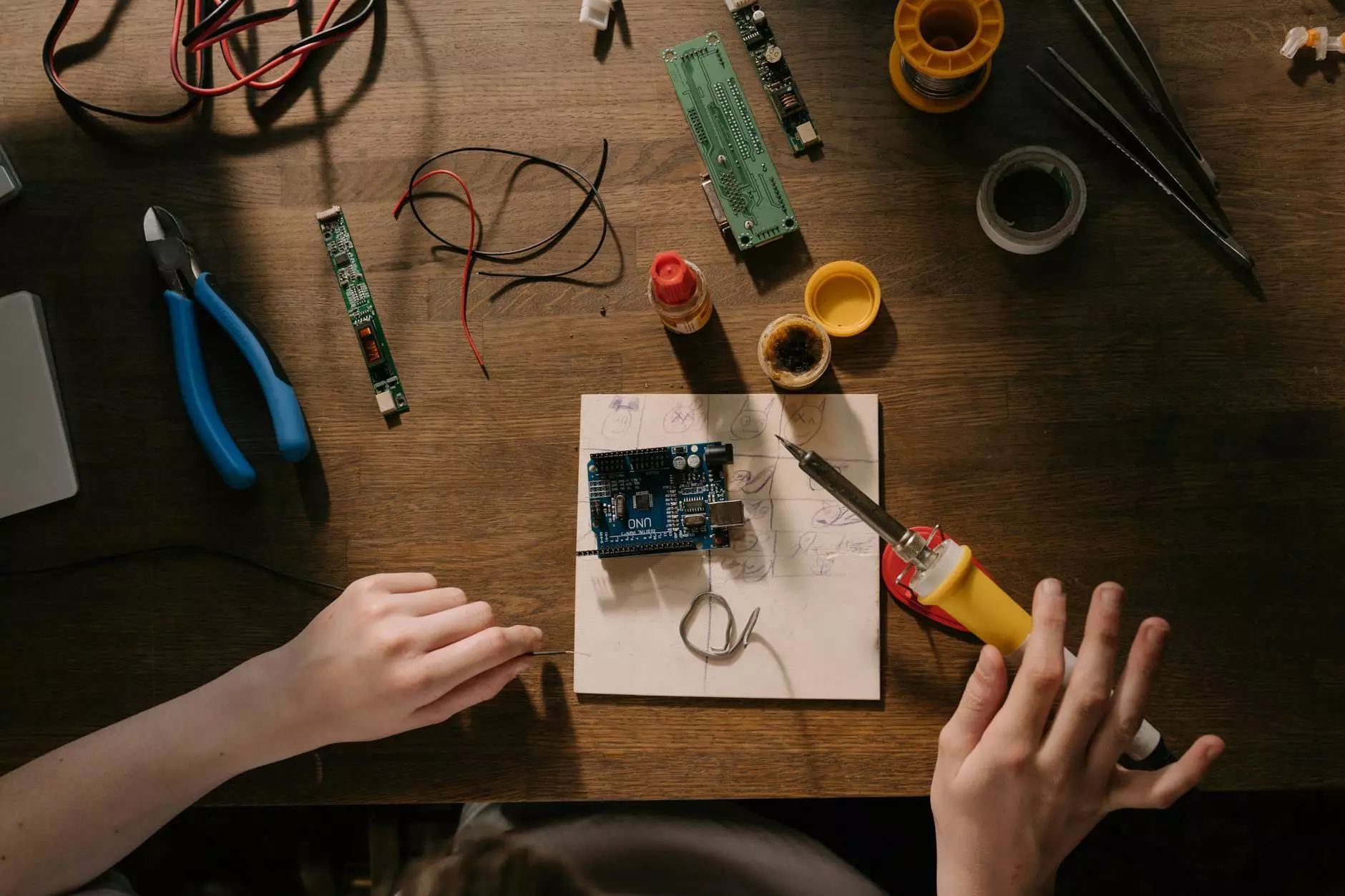
When it comes to soldering electronic components, the presence of voids in the solder joints can be a cause for concern. Voids are essentially empty spaces or gaps within the joint where the solder has failed to completely fill. This can lead to various issues and potentially affect the functionality and reliability of the electronic device.
Understanding the Impact of Voids
Voids in solder joints can negatively impact the electrical and thermal conductivity of the joint. The presence of these voids increases the resistance, which can lead to the generation of heat and potentially result in performance issues or even component failures. In high-power applications or those that require efficient heat dissipation, such as automotive electronics, aerospace systems, or power electronics, voids can significantly hamper the overall performance.
Furthermore, voids in solder joints can affect the mechanical strength and stability of the connection. Solder joints are responsible for not only establishing electrical connections but also for providing mechanical support to the components. Voids can compromise the structural integrity of the joint, making it more susceptible to mechanical stresses, vibrations, and shocks. Over time, this can lead to premature failures, reducing the overall lifespan of the electronic device.
The Causes of Voids in Solder Joints
To address the issue of voids, it's essential to understand the various factors that contribute to their formation. Here are some common causes of voids in solder joints:
- Inadequate soldering temperature and time: Insufficient heating or inadequate soldering time can result in incomplete melting and improper wetting of the solder, leading to void formation.
- Poor solder paste quality: Low-quality solder pastes may contain impurities or excessive flux that can contribute to void formation during the reflow process.
- Inappropriate stencil design: Stencils with improper aperture sizes or inadequate solder paste release can result in uneven distribution of solder, leading to voids.
- Component design and placement: Inadequate component pad designs, such as uneven or improper stencil land patterns, can lead to insufficient solder filling and void formation.
- Insufficient flux activity: Flux plays a crucial role in the soldering process by removing oxides and promoting wetting. Insufficient flux activity can hinder proper wetting and contribute to void formation.
Addressing the Issue of Voids
As the impact of voids in solder joints is well-recognized, several strategies and solutions have been developed to minimize or eliminate their occurrence. Here are some effective ways to address the issue:
- Optimizing soldering process parameters: By carefully controlling factors such as temperature, time, and reflow profile, you can achieve better solder wetting and minimize void formation.
- Using high-quality solder materials: Investing in high-quality solder pastes and fluxes can significantly reduce the likelihood of voids during the soldering process.
- Implementing proper stencil design: Ensuring correct aperture sizes, adequate solder paste release, and appropriate stencil land patterns can promote better solder distribution and minimize voids.
- Improving component design: Collaborating with component manufacturers to optimize pad designs and ensure compatibility with the soldering process can help reduce void formation.
- Utilizing advanced inspection and detection techniques: Employing X-ray inspection and automated optical inspection (AOI) can help identify and mitigate voids early in the manufacturing process.
Conclusion
Voids in solder joints are indeed a significant issue for electronic devices and their overall performance and reliability. By understanding the impact of voids, knowing their causes, and implementing appropriate mitigation strategies, manufacturers can ensure higher-quality soldering and enhance the longevity and effectiveness of electronic components.
At Luxury Ride Dubai, we prioritize precision and excellence in all aspects, including solder joint quality, to guarantee the utmost satisfaction for our customers.