SolderTip #44: IPC Guidelines for Flux Selection and Use
How Can We Help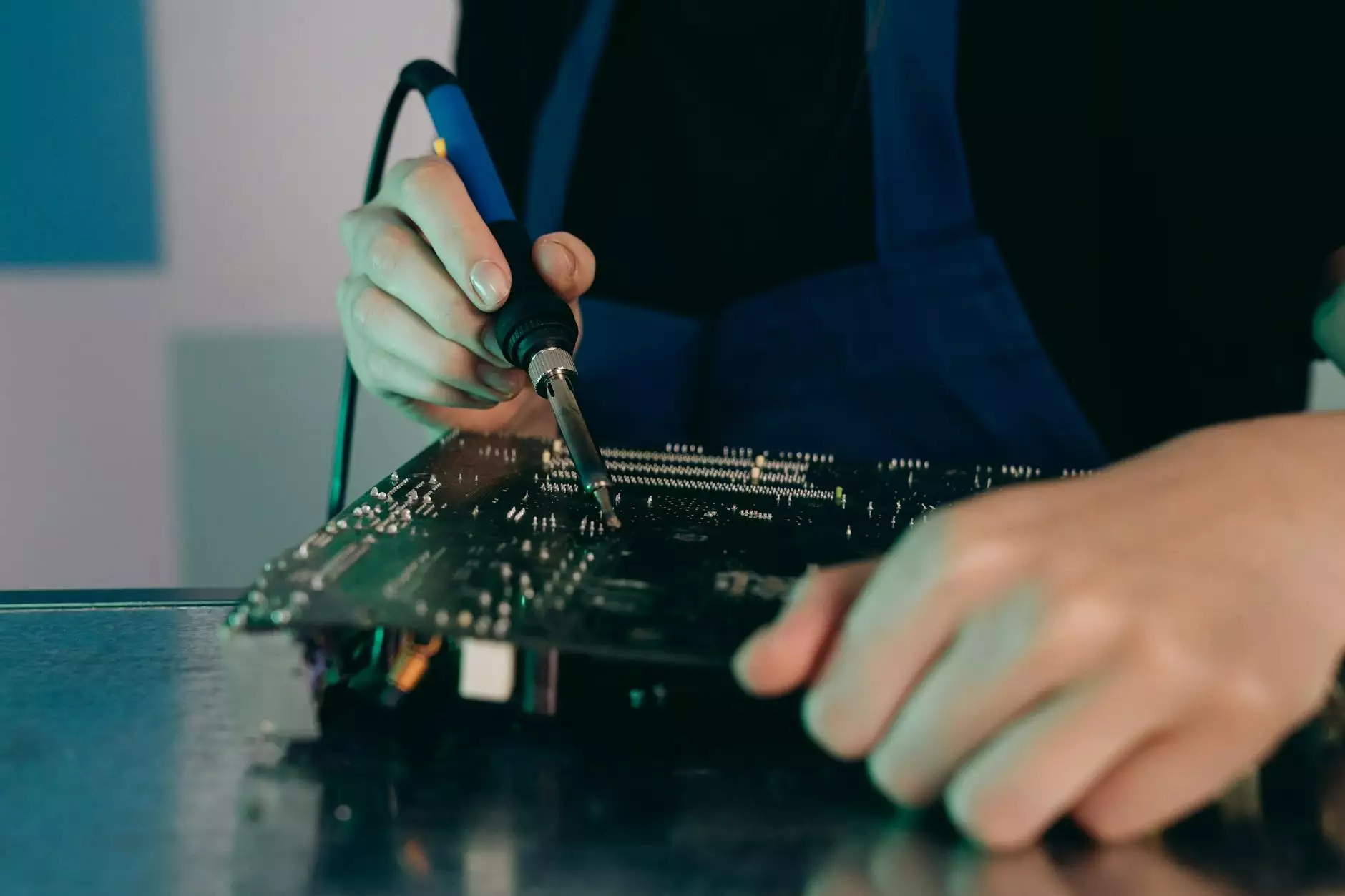
Introduction
Welcome to SolderTip #44, where we will dive into the important topic of IPC guidelines for flux selection and use during soldering.
The Importance of Flux in Soldering
Flux is an essential component in the soldering process as it aids in the removal of surface oxides from the base metals, ensures proper wetting of the solder, and helps achieve strong and reliable solder joints. Proper flux selection is crucial to ensuring high-quality solder connections.
Understanding IPC Guidelines
The IPC (Association Connecting Electronics Industries) provides guidelines and standards for the electronics industry, including recommendations for flux selection and use. Following these guidelines can significantly improve the soldering process and the overall quality of electronic assemblies.
Key Factors in Flux Selection
When selecting flux, several factors need to be considered:
- Compatibility with the base metals
- Process requirements (e.g., reflow or wave soldering)
- Environmental and safety considerations
- Flux residue cleanliness
- Flux activity level
Types of Flux
There are different types of flux available, each with its unique characteristics and applications:
Rosin-Based Flux
Rosin-based flux is one of the most commonly used flux types. It offers excellent thermal stability and is ideal for applications where post-solder flux residue removal is possible.
Water-Soluble Flux
Water-soluble flux is environmentally friendly and allows for easy removal of flux residues using water. It is often used in applications where flux residue removal is required.
No-Clean Flux
No-clean flux is designed to leave minimal residues after soldering. It is widely used in applications where flux residue removal is challenging or not required.
IPC Flux Classification
The IPC provides a classification system to identify fluxes based on their activity level and residues:
- RO (Rosin): Relatively high activity and requires post-solder cleaning
- RMA (Rosin Mildly Activated): Moderate activity and may or may not require post-solder cleaning
- RA (Rosin Activated): Low activity and doesn't require post-solder cleaning
- No-Clean: Minimal activity and doesn't require post-solder cleaning
Guidelines for Flux Selection and Use
Here are some general guidelines to follow when selecting and using flux:
1. Assess the Soldering Process
Consider the specific soldering process being used (e.g., reflow, wave soldering) as this can influence the flux selection. Different processes require different flux properties.
2. Compatibility with Base Metals
Ensure that the flux is compatible with the base metals being soldered. Certain fluxes may not be suitable for specific metal combinations.
3. Environmental and Safety Considerations
Take into account any environmental or safety requirements when selecting flux. Water-soluble fluxes, for example, are more eco-friendly compared to some other types.
4. Flux Residue Cleanliness
Determine the required level of flux residue cleanliness. Some applications may demand thorough removal of flux residues, while others may allow for residues with minimal impact.
5. Consider Flux Activity
Understand the activity level of the flux and choose accordingly. Highly active fluxes may produce stronger joints, but they may also require post-solder cleaning.
In Conclusion
By following IPC guidelines for flux selection and use, you can enhance your soldering process and ensure the production of reliable electronic assemblies. Consider the specific requirements of your application and select the most appropriate flux type to achieve optimal results.
Remember, proper flux selection is crucial for attaining high-quality solder connections and meeting industry standards. If you need further guidance or have specific questions, consult with experts or professionals in the field.